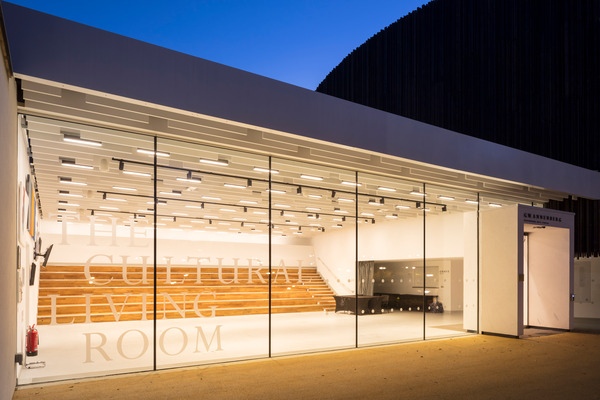
THE PROJECT
Opened by the Duke of Kent in September 2018, the new performing arts centre is a significant upgrade the existing theatre facilities, providing a 926-seat and 1,400 capacity performance space to accommodate a large
range of activities.
The interstitial space between the existing theatre and the new assembly hall will become a new Cultural Living Room (CLR) which will give students an unstructured and informal area for creative output, as well as a flexible social hub for the community of Wellington College.
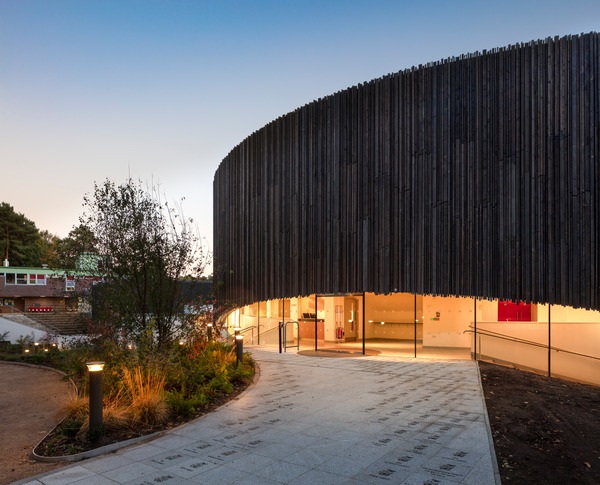
The main auditorium’s circular shape is inspired by historic Grecian amphitheatres, creating a building with no angles: a form that sits softly within the forest landscape.
Designed with high quality acoustics and efficient circulation in mind, this Performance Arts Centre is the venue for students to showcase their creative talents in a formal setting.
The building is steel frame on reinforced concrete pad foundations and slabs. The roof is a single ply membrane flat roof and the external walls are clad in charred timber, with curved clear glass windows around the entrance area and across the two main stair cores.
Attached to the auditorium, the new Cultural Living Room forms a public square between the campus and the forest, connecting the Performance Arts Centre with the existing theatre. This space is not limited by its four walls, rather it is a public space that is vibrant, open, filled with natural light and boasting a large window overlooking the forest.
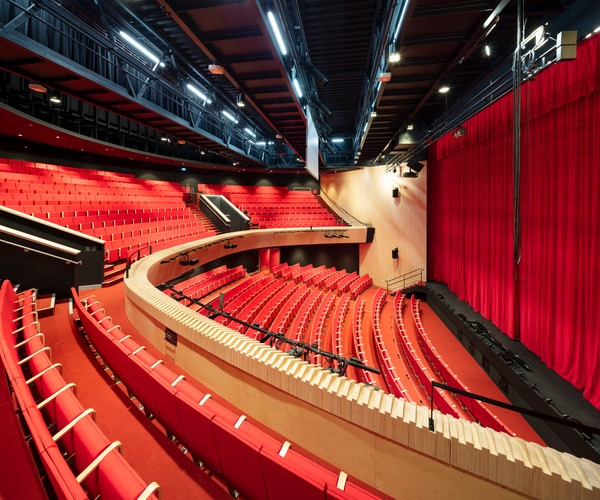
The auditorium balcony fronts have been designed as an evolving surface that reflects and scatters the sound to maximise the theatrical experience.
A reflector ceiling provides first-class acoustic performance, bending both left to right and front to back. Expertly fitted balcony fronts, resembling piano hammers, augment the building’s sonic ambitions.
Cutting edge audio visual facilities were installed to serve the evolving expectations of visitors. During the installation of such essential equipment, we were charged with keeping the technology out of sight, ensuring any experience of the visually stunning building is unimpeded by clutter.
This work was central to delivering a performance space of real excellence for generations of students.

Fronting the campus, a ramp meanders around the theatre’s edge. Meticulously installed Siberian Larch cladding – which will weather in harmony with the surroundings – gives way to a sweeping curve of glass, connecting the building with the surrounding natural landscape.
With the cantilevered steel frame working in tandem with the ground-level glazing, we were able to execute the architect’s vision for a building that, when lit up at night, seems to hover at the heart of its woodland enclave.
£10M
CONTRACT VALUE
76 WEEKS
CONTRACT DURATION
Customer
Wellington College
Enterprises Ltd
Architect
Studio Seilern
Architects
Quantity Surveyor
Thornton Firkin &
Partners
Form of Contract
JCT Design & Build
2011
Live college environment
The approaching road to the site is a farm lane, meaning that the delivery of the steel frame (and all other large deliveries) has had to be carefully coordinated.
Large roof trusses were lifted by crane from within the college grounds, so that we could shorten the truck bed to allow it to fit around the grounds to the site.
The trailer bed could not be shortened prior to coming to site, as it would not have been road legal. We therefore met the lorry at the entrance to the college with a mobile crane.
The plot itself is within a woodland surrounded by trees with tree protection orders
Design changes
At a late stage in the project, the installation of a bar on the first floor was requested, which required a revision of the fire strategy and M & E to the area.
Due to the fast pace of the evolution of cutting edge technology, and to provide the very best experience for end users, late additions to the AV design were also incorporated.
Value Engineering
We changed the design concept to remove the need for a basement.
In place of a basement with plant room and ducts feeding from this, we formed in-situ concrete ducts and stored the air handling unit outside the building footprint, saving the need for a basement.
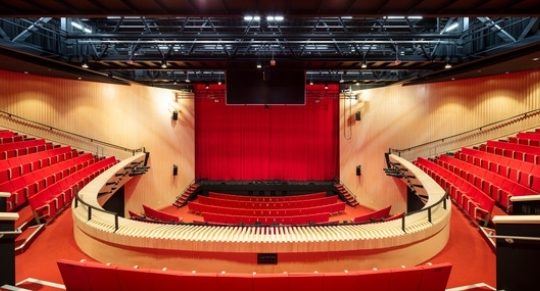
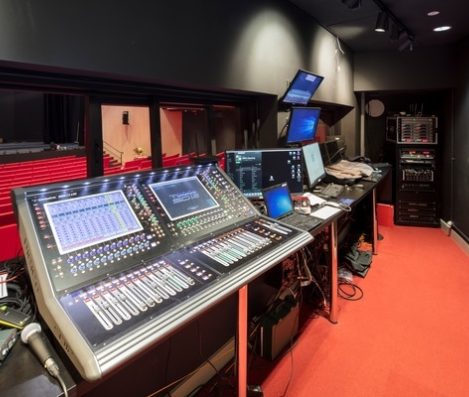
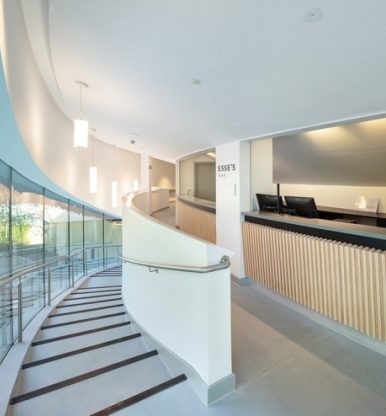
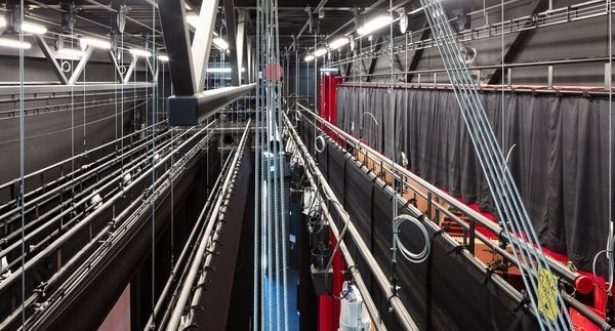